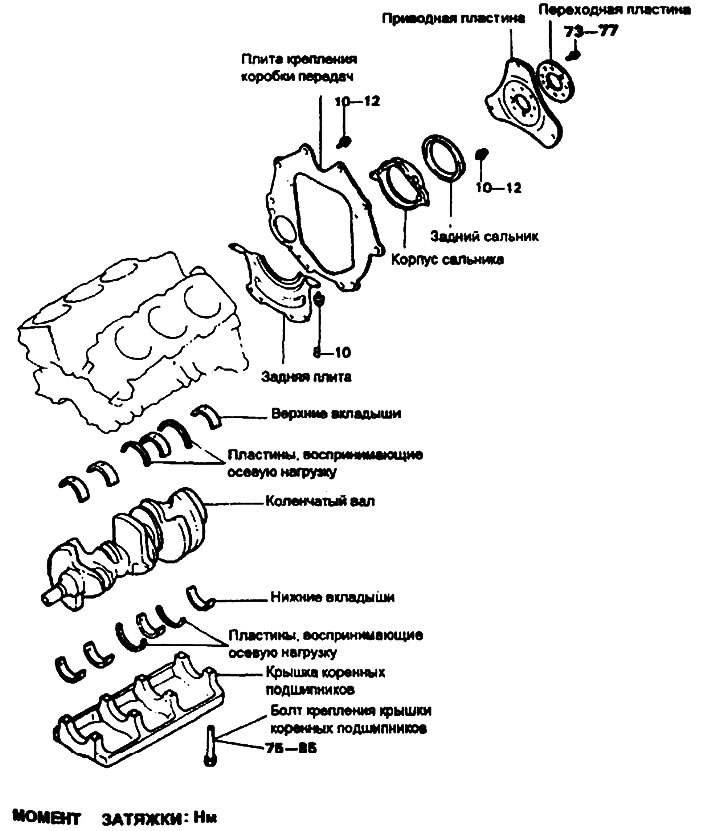
Withdrawal
1. Remove the toothed belt, cylinder head and drive plate, transmission mounting plate, oil pan.
2. Remove the stuffing box and rear oil seal.
3. Remove the connecting rod caps.
Note. Mark the main bearing caps so that they can be reinstalled in the correct direction.
4. Remove the main bearing caps and crankshaft. Lay out the liners according to the numbers of the bearing caps.
Examination
Crankshaft
1. Check the crankshaft main journals and connecting rod journals for damage, uneven wear and cracks. Also check the cleanliness of the oil holes. Repair or replace any defective parts.
2. Check the main journals and connecting rod journals for out-of-roundness and taper.
Rated values:
- Crankshaft journal diameter - 59.980-60.000 mm
- Crankshaft journal diameter - 49.980-50.000 mm
Inserts of main and connecting rod bearings
Visually inspect each bushing for peeling, melted areas, nicks, and bad contacts. Replace defective earbuds.
Oil clearance measurement
Check the oil clearance by measuring the diameter of the crankshaft main journal and the inner diameter of the bearings. The gap is obtained by calculating the difference between the measured diameters.
Rated value:
- Oil clearance
- Indigenous liners of a cranked shaft — 0,02-0,048 mm
- Inserts of the lower head of the connecting rod - 0.02-0.046 mm
Method of using plastic template
A plastic template can be used to measure gaps.
1. Remove oil, grease and dirt from bearings and crankshaft journals.
2. Cut off a piece of plastic template with a length equal to the width of the liner and place it along the axis of the crankshaft journal away from the oil holes.
3. Install the crankshaft, liners and bearing caps and tighten them to the required torque. When performing this operation, do not rotate the crankshaft. Remove bearing caps. Using the scale printed on the template package, measure the thickness of the plastic template at its widest point.
If the gap exceeds the allowable limit, the liners should be replaced or smaller repair liners should be used. When installing a new crankshaft, use liners of nominal size.
![]() | ![]() |
If even when changing the liners it is not possible to obtain the nominal value of the gap, the liners of the corresponding repair size should be ground.
Stuffing box
Check the front and rear oil seals for damage and lip wear. Replace defective seals.
Drive plate
Replace warped, damaged or cracked drive plate.
Installation
Indigenous liners
1. Install the main bearing with a groove in the bed of the cylinder block.
2. Install the main bearing without groove into the bed of the main bearing cap.
3. Install the crankshaft. Apply engine oil to the main and connecting rod journals.
4. Bearing caps should be installed with the arrows pointing towards the front of the engine. Make sure that the caps are positioned correctly according to their numbers.
5. Torque tighten the bearing cap bolts.
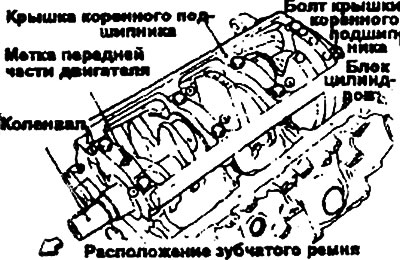
- Tightening torque: Main bearing cap bolts - 75-85 Nm.
7. Cover bolts should be tightened evenly in 4 or 5 steps until the required tightening torque is reached.
8. Check that the crankshaft rotates easily and has normal end play.
Axial play of the crankshaft:
- Nominal - 0.05-0.25 mm
- Limit - 0.3 mm
9. Using a special tool (09321—33000), install the rear oil seal into its housing.
![]() | ![]() |
10. Apply sealant to the surfaces shown in the illustration. Install the seal assembly to the cylinder block.
- Tightening torque: Stuffing box bolts - 10-12 Nm.
11. Tighten the gearbox mounting plate to the required torque.
- Tightening torque: Bolts of the gearbox mounting plate - 10-12 Nm.
12. Tighten the drive and adapter plate bolts.
- Tightening torque: Drive and adapter plate bolts - 73-77 Nm.
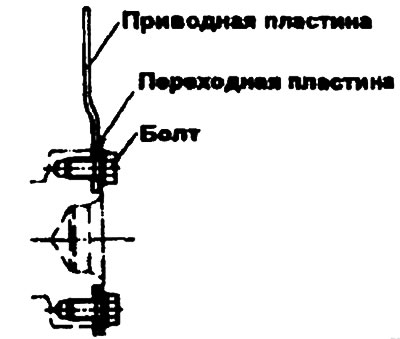