Withdrawal
1. Using a special tool (09222—21001), remove the crackers. Remove the top poppet, valve spring, bottom poppet and valve.
Note. Lay out all the removed parts in the order in which they should be installed in their places.
2. Use pliers to remove the sealing caps.
Warning. Do not reuse them.
![]() | ![]() |
Examination
Valve bushings
Check clearance between valve stem and bushing. If this clearance exceeds the allowable value, replace the valve bushing with a new one.
Clearance between valve stems and sleeve:
Rated value:
- Inlet valve - 0.03-0.05 mm
- Exhaust valve - 0.05-0.09 mm
Limit value:
- Inlet valve - 0.10 mm
- Exhaust valve - 0.15 mm
Size, mm | Dimension mark | Hole diameter in the cylinder head, mm |
0,05 OS | 5 | 13,050-13,068 |
0,25 OS | 25 | 13,250-13,268 |
0,50 OS | 50 | 13,500-13,518 |
OS - Increased size.
Valve springs
1. Check the free height of each valve spring and replace if necessary.
2. Using a square, check the perpendicularity of the ends of each spring to its axis. If the deflection is excessive, replace the spring.
Rated value:
- Free length - 49.8 mm
- Force - 329 N / 40.4 mm
- Deviation from squareness - Maximum 2°
Limit value:
- Free length - 48.8 mm
- Force - 329 N / 41.4 mm
- Deviation from squareness — Maximum 4°
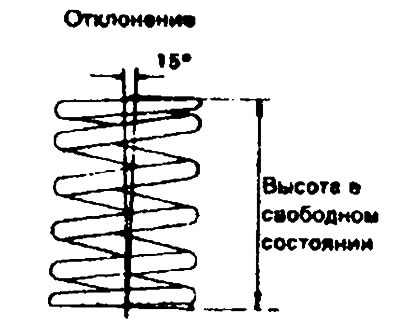
Valve seat rebuild
1. When repairing, check the valve bushing for wear. Replace the worn bushing and then repair the valve seat.
2. Fix the valve seat using a valve seat cutter and accessory tool.
3. After repair, the valve and its seat must be lapped using lapping paste.
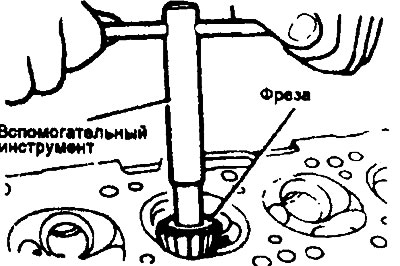
Valve seats
1. Check the valve seat for signs of overheating and improper contact with the valve faces. Repair or replace the valve seat if necessary.
2. The width of the valve seat contact strip must be as specified.
Valve seat contact strip width:
- Inlet valve - 0.9-1.3 mm
- Exhaust valve - 1.2-1.6 mm
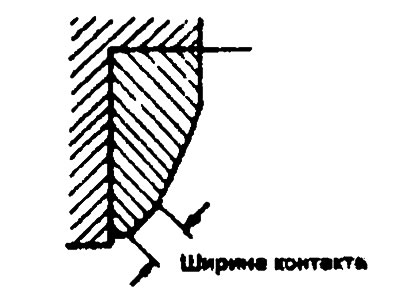
Installation
1. Install the lower spring plates.
2. Using a special tool (09222—32100), push the bottom plate back into place slightly. The sealing cap is installed in its place using a special tool.
Warning:
- Do not reuse old sealing caps.
- Improper seating of the sealing cap will cause it to become eccentric and result in oil leakage along the valve stem.
3. Lubricate each valve with engine oil. Install the valves in the bushings. Do not force the valves into the sealing caps. After installation, check the smooth movement of the valves.
4. Valve springs are installed with the enamelled side towards the top poppets.
![]() | ![]() |
5. Using a special (09222—21001) or other appropriate tool, compress the spring and install the cotters. After installing the valves, check the correct installation of the crackers.
Warning. When compressing the spring with a valve spring compressor or a suitable tool, make sure that the sealing cap is not compressed by the bottom of the upper spring cup.
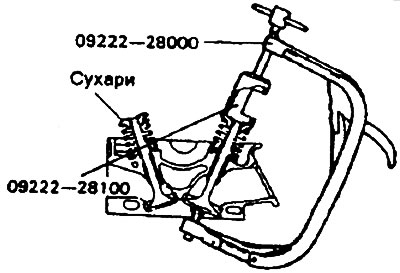