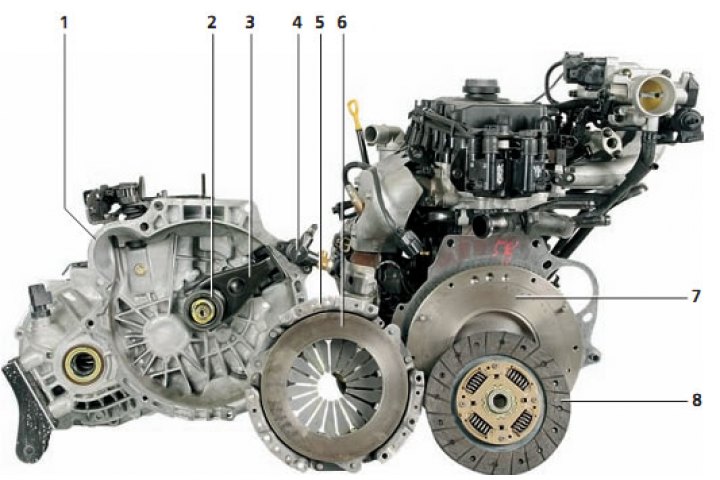
Clutch elements: 1 - clutch housing; 2 - clutch release bearing; 3 - clutch release fork; 4 - working cylinder of the hydraulic clutch; 5 - clutch cover; 6 - pressure plate; 7 - flywheel; 8 - a driven disk with a spring damper of torsional vibrations
Tightening torques for threaded connections, N·m
Bolt of fastening of a pedal to an arm | 25–35 |
Bolt of fastening of the main cylinder to an arm of a pedal | 17–26 |
Union nut for fastening the pipeline | 13–17 |
pipeline holder | 4–6 |
Bolt of fastening of the working cylinder | 15–22 |
Hollow bolt for fastening the pipeline to the working cylinder | 25 |
Bolts of fastening of a casing of coupling | 15–22 |
Nut of fastening of a pusher of the main cylinder to a pedal | 9–14 |
Nut of fastening of the switch of blocking of ignition | 8–10 |
Technical specifications
Clutch drive type | Hydraulic |
Driven clutch disc | Dry, diaphragmatic |
Outer/inner diameter of driven disk, mm | 215/145 |
Clutch cover assembly with pressure plate | With diaphragm pressure spring |
Inner diameter: working cylinder, mm master cylinder, mm | 20,64 15,57 |
Data for checks and adjustments
Clutch drive type | Hydraulic |
Driven plate thickness (in a free state) mm: engines 1.3; 1.5 and 1.6 l engine 1.1 l | 8,5±0,3 8,0±0,3 |
Clutch pedal free travel, mm | 6-13 |
Clutch pedal height above the floor, mm | 160,7 |
Clutch pedal travel, mm | 140 |
Clearance between the working cylinder and the piston, mm | 0,15 |
Clearance between the main cylinder and the piston, mm | 0,15 |
Applicable lubricants
Place of application | Name |
Fork contact surface with clutch release bearing | CASMOLY L9508 |
Inner surface of the clutch release bearing | CASMOLY L9508 |
The mirror of the working cylinder, the outer surface of the piston and the cuff | Brake fluid DOT-3 or DOT-4 |
Clutch disc splines | CASMOLY L9508 |
Mirror of the main cylinder and the outer surface of the piston | Brake fluid DOT-3 or DOT-4 |
Master cylinder tappet, pusher pin and washer | Wheel Bearing Grease SAE J310a, NLGI No.2 |
Clutch pedal axle and bushings | SAE J310a Chassis Lubricant, NLGI-No.1 |
The contact surface of the clutch release fork with the pusher of the working cylinder | CASMOLY L9508 |
General information
The clutch is located between the engine and the gearbox and is designed to disconnect and connect the flywheel located on the engine crankshaft and the gearbox input shaft.
The clutch consists of a driven (frictional) disc, clutch cover with pressure plate and diaphragm spring, and clutch release mechanism. The friction disc consists of two annular friction linings, which are mounted on the hub through damper springs.
The diaphragm spring mechanism creates a force that combines the work of the flywheel, pressure and driven discs to ensure joint rotation, in this case the clutch is engaged and transmits torque from the engine to the gearbox. The clutch is controlled by the clutch pedal.
The clutch is released as follows. As a result of pressing the clutch pedal, the piston in the master cylinder moves, compressing the fluid, the pressure of which is transmitted through the hose to the clutch slave cylinder, the piston of which, in turn, acts on the clutch release fork. The release fork moves the release bearing, which presses on the center of the diaphragm spring, thereby releasing the engagement force around the perimeter of the spring and moves the pressure plate backwards. This releases the driven disk, after which the motor shaft and gearbox shaft can rotate independently of each other.
Friction linings are fixed on both sides of the driven disk. The leading part of the disc is connected to the hub through the parts of the torsional vibration damper, which provides an elastic connection between them. Vibration damper reduces dynamic loads that cause twisting (unwinding) transmission shafts, which occur when the vehicle speed changes sharply, hits bumps in the road, when the clutch is suddenly engaged, and also due to uneven engine torque. Elastic vibrations of transmission parts lead to the appearance of noise in mechanisms and units, as well as to vibrations, as a result of which damage to parts is possible if the amplitude of elastic vibrations reaches significant values. An absorber serves to absorb the energy of elastic torsional vibrations.
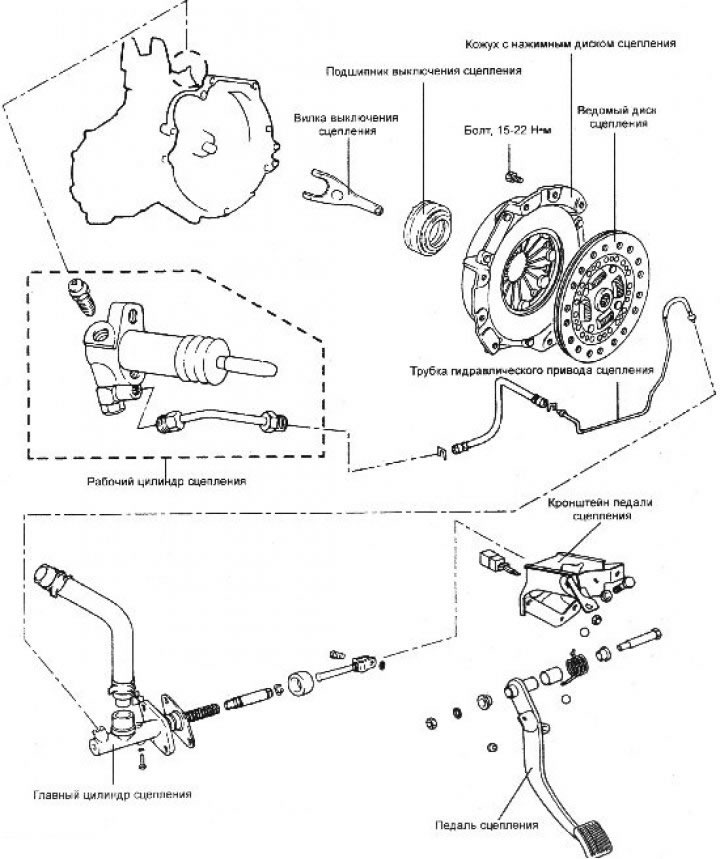